
如何選擇車用壓力感測器??
The engine test
stands used with advanced data-acquisition systems require a
different type of pressure sensor than those used in the
past. Engine hydraulics and pneumatics operate faster and
often, with higher pressures and temperatures. Accordingly,
the pressure sensors have to be more reliable and rugged in
order to reduce downtime.
In choosing the
correct pressure sensor for your application, you must
consider several specifications. You must decide which type
of pressure sensor will give you the best results in your
application.
There are five
basic types:
-
Gage pressure sensors【表壓感知器】
- With gage sensors, pressure readings are referenced to
the atmosphere. That is, zero output is at atmospheric
pressure. You use this type of sensor when you need to
measure both vacuum (negative output) and pressure
(positive output).
-
Vacuum pressure sensors
【真空壓力感知器】-
A vacuum sensor's output is zero at atmospheric
pressure, like the gage sensor, but the output increases
as vacuum increases. You calibrate vacuum sensors so
their output becomes more positive as the pressure
becomes more negative.
-
Differential Pressure Sensors【差壓感知器】
- This type of sensor has two pressure ports, as shown
in Figure 1, and senses the difference in pressure
between the two ports. You can use differential pressure
sensors to measure the pressure of liquids or gasses.
-
Absolute Pressure Sensors【絕對壓力感知器】
- The reference for this type of sensor is full vacuum.
That is, the output is zero at full vacuum. Note that
there is no polarity change when the input pressure
changes from vacuum to pressure above atmosphere.
-
Barometric pressure sensors【大氣壓力感知器】
- Barometric pressure sensors are absolute pressure
sensors with a limited range. Usually, the output of
these sensors is expressed as "inches of Mercury (Hg),"
and the output ranges are 16-32-in. HgA or 26-32-in. Hg
with zero output at the low number. A standard
"absolute" sensor may be used over 0-30-in. HgA range,
but the limited range offers more resolution, especially
with a voltage output for the typically small barometric
pressure changes. You may use several different types of
pressure transducers in a typical engine test stand.
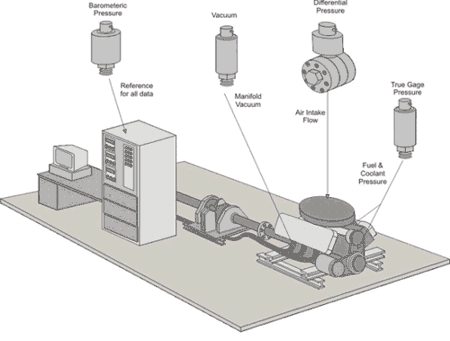
Gage pressure
sensors【表壓力感知器】:
-
Engine oil pressure.【機油壓力感知器】
To ensure lubrication system integrity, you often want
to correlate oil pressure with time and crankshaft
position.
-
Coolant pressure.【水箱壓力感知器】
Coolant pressure is a measure of how well the cooling
system is working.
-
Fuel pressure.【燃油壓力感知器】
You measure fuel pressure during fuel pump and pressure
regulator tests.
-
Cylinder compression (cold test).
【汽缸壓力感知器】To
measure this parameter, you insert a gage sensor into
each cylinder's spark plug hole. By correlating cylinder
pressure with cranking torque, crank angle, and timing,
you can detect piston ring, valve, or crank problems.
-
Pressure decay. By measuring
how quickly the pressure decays inside a pressurized
cavity, you can detect damaged or missing gaskets and
O-rings, emission valve problems, and other leaks. You
also can use a differential pressure sensor to measure
pressure decay.
Vacuum pressure
sensors【真空壓力感知器】:
Differential
pressure sensors【差壓感知器】:
-
Fluid flow.
【液體】Using
a precision calibrated orifice or Venturi tube, and
measuring the differential pressure across the orifice,
you can measure intake airflow or engine coolant flow.
The advantage of using a differential pressure sensor
for this measurement instead of two gage sensors is that
accuracy is always specified as a percentage of the
sensor's full-scale reading. By using a differential
pressure sensor, the full-scale reading can be much
smaller, thereby reducing measurement error
-
Dry airflow.
【氣體】You
need to measure dry airflow when testing engine-block
oil ports. You can correlate the back pressure with
crankshaft position to find missing main bearings or
plugged oil cavities.
You also can use
a differential pressure sensor as a gage sensor inside a
closed test chamber; you must vent the low or negative
pressure port to the outside atmosphere rather than vent it
inside the test chamber where the ambient pressure may be
different or variable. The wet/wet characteristics of the
differential pressure sensor offers environmental protection
and reliable operation.
Absolute
pressure sensors【絕對壓力感知器】:
You use absolute
pressure sensors when you have a data acquisition system
that can only accept unipolar inputs. In this case, you
would use an absolute pressure sensor in place of a gage
sensor or vacuum sensor.
Selecting the
Right Pressure Sensor
The Pressure
Sensor Selection Checklist lists the specifications you must
consider when choosing a pressure sensor. The most important
specifications are electrical output, accuracy, operating
environment, and mechanical coupling.
Electrical
output【電子訊號輸出】
Pressure sensors
are available with either voltage outputs or current
outputs. Strain-gage sensors usually have output ranges of
0-30 mV or 0-100m V, depending on the type of strain gage
they use. Sensors using bonded metal strain gages have the
lower output, but you can use them over a wide temperature
range-often as low as cryogenic temperatures and some up to
450E°F. Sensors using piezoresistive strain gages offer
higher output voltages, but they have a more limited
operating temperature range.
Some sensors
have an internal amplifier that provides a 5-VDC or 10-VDC
output.
The advantages
of using these sensors include output signal levels that are
above the noise level, internal zero and span adjustments
for a precise setup, and three-wire connections instead of
the four-wire connections needed for millivoltoutput
sensors. Unfortunately, the internal amplifiers used to
boost the output signal limit the frequency response of
these sensors to approximately 3 kHz. They also cost more
and have narrower operating temperature ranges than
millivolt-output sensors.
Current output
sensors are two-wire sensors with a 4-20 mA output.
They offer high
noise immunity and can be located further from the
data-acquisition system than voltage output sensors can.
Frequency response is in the 2.5-3.0 kHz range, and they
have zero and span adjustments for precise setup.
Accuracy【精度】
Accuracy is the
most important performance specification. Sensors with
accuracies of 0.05% full scale are available, as are
accuracies of 0.1 %, 0.25%, and 0.5%. Price and availability
are inversely proportional to the accuracy of the sensor, so
you can save time and money by not specifying a sensor that
is more accurate than you really need.
Operating
Environment【工作環境】
You also need to
consider where you will use the sensor. The amount of
protection the sensor will need depends on whether the
sensor is indoors and dry or outside and exposed to the
elements. Obviously, the cost of a sensor designed for use
in a harsh environment will be higher than a sensor used in
a benign environment.
The operating
environment also will determine the type of connectors and
cabling you will need. Quick-disconnect electrical
connectors make it easy to remove sensors for periodic
calibration, but most cannot be used outdoors.
Waterproof
connectors rated for outdoor use are costly in comparison.
Some sensors
come with an integral cable. A sealed boot on the sensor
protects the cable. When equipped with an atmospheric vent
tube inside the cable jacket, these sensors are submersible.
Mechanical
Coupling【安裝】
You also need to
consider how you will couple the sensor to the test system.
Sensors are available with a variety of threaded options,
including English threads, metric threads, SAE tube
connections, and pipe threads. Most pressure sensors made
for test and measurement applications are built with
stainless steel wetted parts. The wetted part of the sensor
is the pressure port that will come in contact with the
measured media (fluid or gas). Welded stainless steel is one
of the most trouble-free materials, as is a combination of
stainless steel and hastelloy. A completely welded assembly
built without the use of epoxies, sealants, or O-rings
ensures long-term stability and hassle-free use.
Finally,
consider ease of installation and calibration. If you are
using sensors that use strain-gage technology, the best
option is to purchase one with a built-in shunt calibration
circuit. The shunt calibration circuit provides a calibrated
output without your having to apply a known pressure source
to the sensor. By removing the system pressure and venting
the sensor to the atmosphere on a gage type pressure sensor,
you can adjust the sensor's output to zero. Then, by
engaging the shunt calibration circuit, you can calibrate
the full scale reading.
If you prefer,
however, to have a calibration lab check and calibrate your
sensors, this service is readily available from
manufacturers and third-party labs. If your sensors are
going to be out of service for any length of time, you
should consider purchasing spare sensors.
|